前回、PVT特性のグラフをご紹介しました。これを活用しながら、体積変化挙動を考察します。下図は、前回の図に、私が(赤色部分を)加筆しております。
代表的な成形条件は、
PSの場合、樹脂温度200℃、射出圧力80MPa
PEの場合、樹脂温度200℃、射出圧力40MPa
程度です。この条件で型内に注入された樹脂は、常温常圧、すなわち25℃、0MPaでの体積へと変化します。体積収縮です。
それぞれの体積収縮率を計算すると比容積(比重の逆数)の変化より
PSの場合、 0.99 → 0.96 約3%
PEの場合、 1.29 → 1.06 約18%
となります。結晶性樹脂のPS(PPもおおよそ同様)の場合、約2割近くも体積が減ることとなります。ちなみに、PSではわずか3%です。
一時期、非晶性樹脂のABSを使用した自動車の塗装外板の成形にたずさわってましたが、PPバンパーでの経験に比べて、面品質の確保は圧倒的に楽であったことを思い出します。まさにこの体制縮率の影響でした。
さて、2割も体積収縮してはまったく面品質を確保できないので、体積収縮分の樹脂の補給が必須となります。射出成形工程の保圧のプロセスが極めて重要です。
図は、射出成形工程の説明図です。この中の③保圧の工程です。
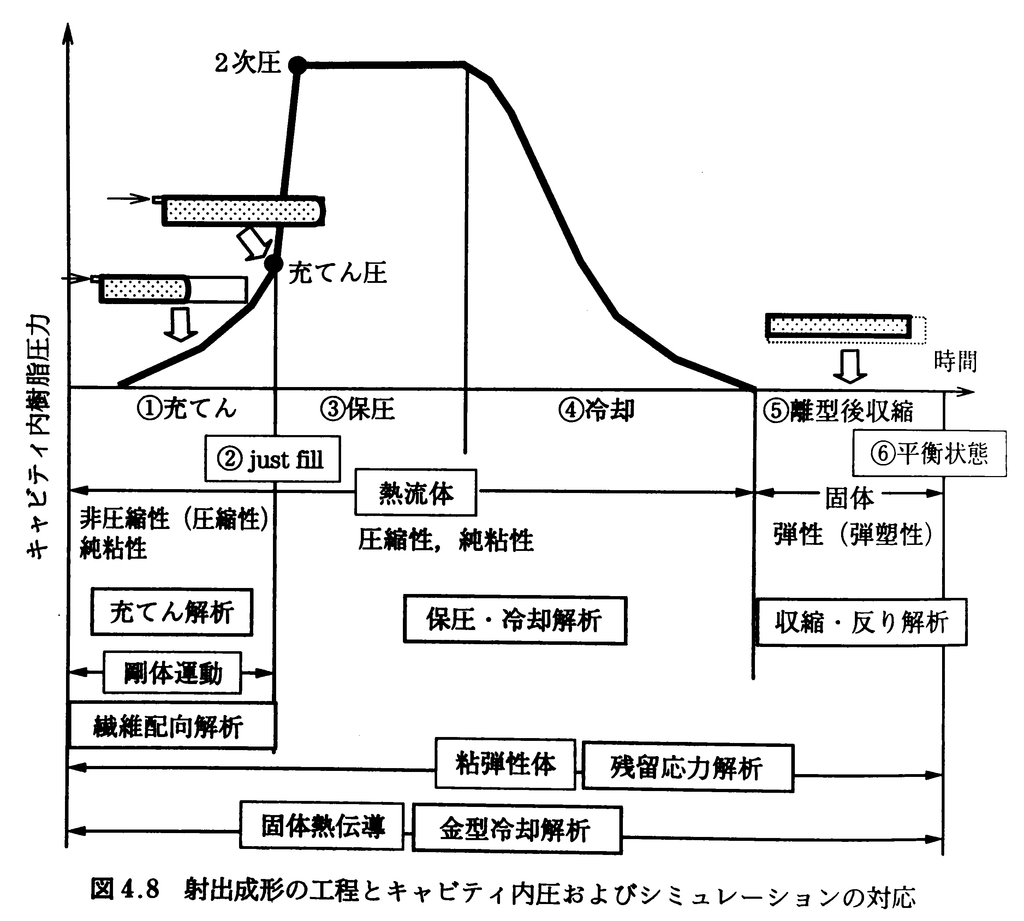
上図は、以下の書籍からの引用です。
日本塑性加工学会編集 コロナ社刊行 「流動解析― プラスチック成形」 p.50
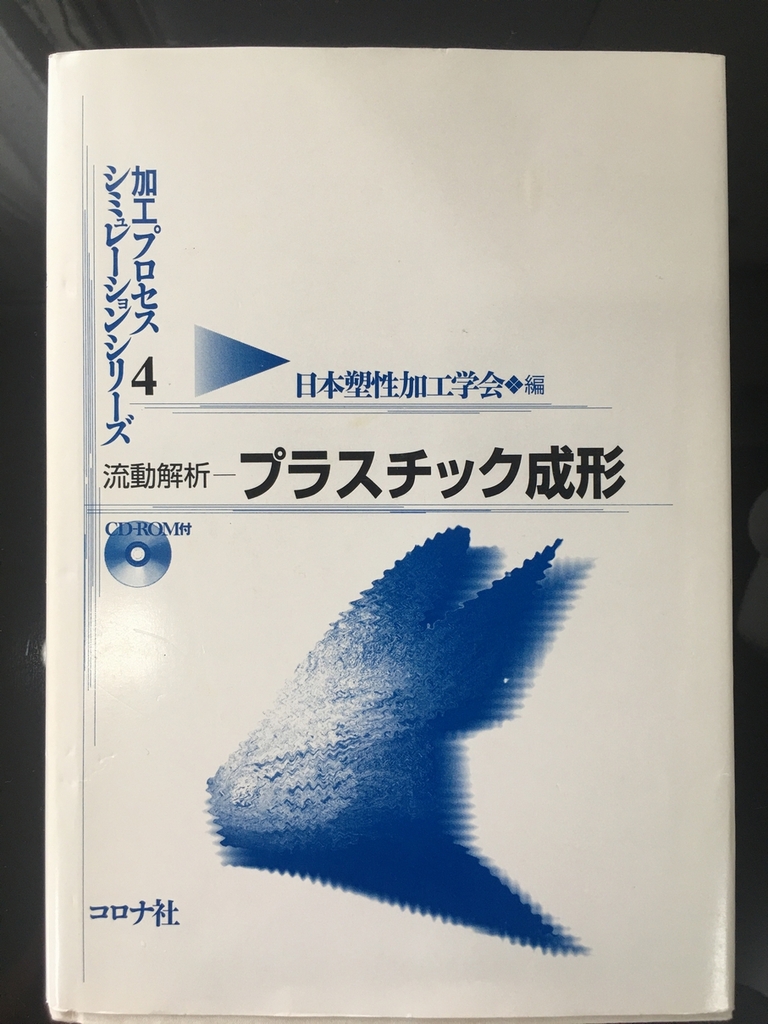
体積収縮分の樹脂を補うために、保圧で圧を掛け、収縮分を逐次補給します。
しかし、現実には2点ほど問題を生じます。
ひとつは、保圧の際の樹脂圧力に金型が負けて、型開き現象を生じ、バリが発生するという現象です。理論的には十分な型閉じ圧力という場合でも、成形機の経年劣化や、射出型の加工精度等々の問題で問題を生じることとなります。この対応としては、経験的なマージンを持った型締め能力で準備することが必要となります。
もう一点の困った現象は、保圧の際の樹脂の補給路が閉じてしまうという問題です。あたりまえですが、どんなに圧力を掛けても、流路が閉じてしまってはどうにもなりません。この対応としては、冷却固化の際にも流路が確実に保てるような製品形状設計と型仕様設定(多くの場合は両方の組み合せ)の事前検討で対応します。
この件の具体的対応方法は、次回ご説明します。